Why Is My Exterior Concrete So Damaged? Salt Damage & How to Protect Against It
- James Walther
- Apr 1
- 10 min read
Seeing the Damage Firsthand

You walk out to your driveway one spring morning and stop cold. The concrete looks rougher than usual—like it’s been sandblasted. Patches are flaking off near the edges, small pits have formed near the surface, and there’s this white, crusty stuff in the cracks. You might even spot chunks missing from your steps or patio. It’s not just wear and tear anymore—your concrete is crumbling.
And it’s happening faster than it should.
This kind of damage is all too common across Northern BC, especially after one of our long, wet winters. We’ve had plenty of folks from around the area—whether it’s by the coast or a little farther inland—reach out asking why their concrete is breaking down when it’s barely a few years old. Maybe it started as a few hairline cracks or some surface chipping. But once the damage kicks in, it doesn’t take long to snowball into something bigger.
Here’s the real kicker: Most of the time, it’s not the concrete’s fault. It’s the salt.
Those de-icing products we rely on to keep walkways and driveways safe? They’re doing a number on our concrete. And while the effects might seem subtle at first, year after year, they add up to major deterioration.
So what’s really going on here? Why does salt—something we trust for safety—end up destroying exterior concrete surfaces? Let’s break it down and look at what’s happening under the surface.
What Salt Actually Does to Concrete
Here’s the truth most people don’t hear until it’s too late: salt doesn’t just sit on the surface of your concrete—it goes to work the moment it touches moisture. And in northern BC, moisture is never in short supply.
When we talk about “salt,” we’re usually referring to de-icing salts—calcium chloride, magnesium chloride, sodium chloride. These are great for melting ice, but brutal on concrete. The main culprit? Chloride ions. These tiny particles don’t just sit there harmlessly—they penetrate the surface and break down the very glue that holds your concrete together: the cement paste.
And it’s not just chemical damage. Salt attracts water. It pulls moisture deep into the concrete slab—just in time for the next freeze-thaw cycle (more on that in a minute). That moisture expands when it freezes, and now you’ve got internal pressure building up from the inside out. The result? Flaking, chipping, cracking. Once that outer surface is compromised, the cycle repeats faster every year.
Even when the slab looks dry, salt left behind can continue working below the surface. And the more damage that’s done, the more vulnerable the slab becomes to the next round of moisture and freezing.
One misconception is that concrete is invincible outdoors. It’s not. Even high-strength mixes are still porous unless properly sealed. Once salt gets into unsealed or poorly finished concrete, the damage can accelerate quickly—especially over repeated winters.
If your concrete is already showing signs of wear—like light pitting, surface discoloration, or minor flaking—it’s very likely that de-icing salts are a major contributing factor. Left untreated, that damage will continue to deepen year after year.
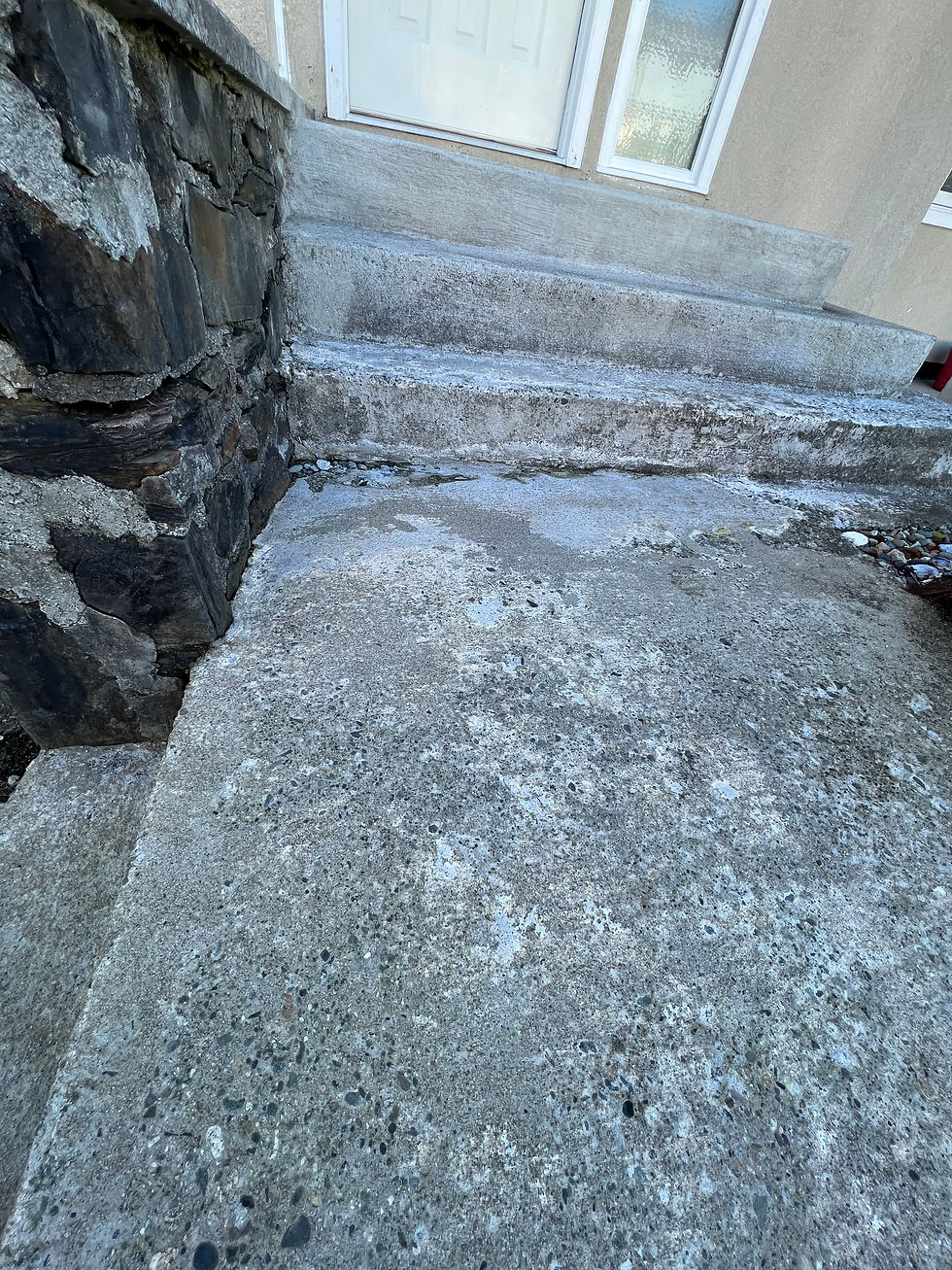
The Role of Freeze-Thaw Cycles
Salt may start the damage, but freeze-thaw cycles are what take it to the next level—and in regions like northern BC, they’re unavoidable. That repeated pattern of freezing, thawing, and refreezing is one of the most destructive forces concrete faces outdoors.
Here’s what’s happening below the surface: Concrete is porous. Even if it looks smooth, it’s full of tiny voids that absorb water. When temperatures drop, that water freezes and expands by about 9%. That expansion creates internal pressure, pushing outward from inside the slab.
Now imagine that happening dozens of times a season. Northern climates don’t just dip below freezing—they bounce above and below it constantly during late fall, winter, and early spring. Every one of those freeze-thaw cycles puts additional stress on the concrete.
Salt makes this process worse. It lowers the freezing point of water, so instead of one long freeze, you get more frequent freeze-thaw events. Water melts during the day, seeps deeper into the concrete, and then refreezes at night. Over time, that repeated expansion and contraction causes the surface layer to weaken, flake off, and expose the aggregate underneath.
Even if the concrete is structurally sound, surface degradation from freeze-thaw can drastically shorten its lifespan. Once the protective top layer is compromised, water intrusion becomes faster and more aggressive, and the damage accelerates from one season to the next.
This is why freeze-thaw resilience is critical in any exterior concrete work in colder climates. If the slab isn’t sealed, finished properly, or made with the right air-entrained mix, it’s only a matter of time before the surface starts to break down—especially when salt is in the mix.
Other Contributors to Exterior Concrete Damage
Salt and freeze-thaw cycles are a brutal combo, but they’re not acting alone. If your exterior concrete is falling apart faster than expected, chances are there are other contributing factors at play—some of which go all the way back to how the concrete was installed.
1. Poor finishing practices. If the surface was overworked or troweled too tightly during installation, it can seal off the top and trap bleed water just beneath. That leads to a weak surface layer that’s prone to flaking—especially under winter conditions.
2. Inadequate air entrainment. For northern climates, concrete should be air-entrained. That means intentionally adding microscopic air pockets to give freezing water somewhere to expand without building destructive pressure. If the mix didn’t include the right admixtures—or if too much water was added on-site—those protective air voids are compromised or lost entirely.
3. Low-strength or poorly cured concrete. For exterior flatwork in cold climates, concrete should hit a minimum of 32 MPa compressive strength. If the mix was too weak or didn’t cure properly (especially in cold weather), it becomes more porous and less resistant to salt and moisture intrusion.
4. Lack of sealing or expired sealers. Concrete isn’t naturally waterproof. Without a penetrating sealer, moisture—and everything it carries—can migrate freely in and out of the slab. Even if it was sealed once, that protection doesn’t last forever. If it hasn’t been resealed in several years, that barrier is long gone.
5. Physical wear and abrasion. Snow removal blades, studded tires, foot traffic with grit, and even hard-bristle brooms can wear down the surface layer over time. Once the finish starts breaking down, it exposes the slab to more water intrusion—and the damage cycle kicks into high gear.
The reality is, exterior concrete is constantly under attack from multiple angles. Salt just speeds up the process. If the slab wasn’t built to handle northern BC conditions—or hasn’t been properly maintained—it’s only a matter of time before the surface starts to give out.
But the good news? With the right protection strategy, you can break that cycle and dramatically extend your concrete’s life.
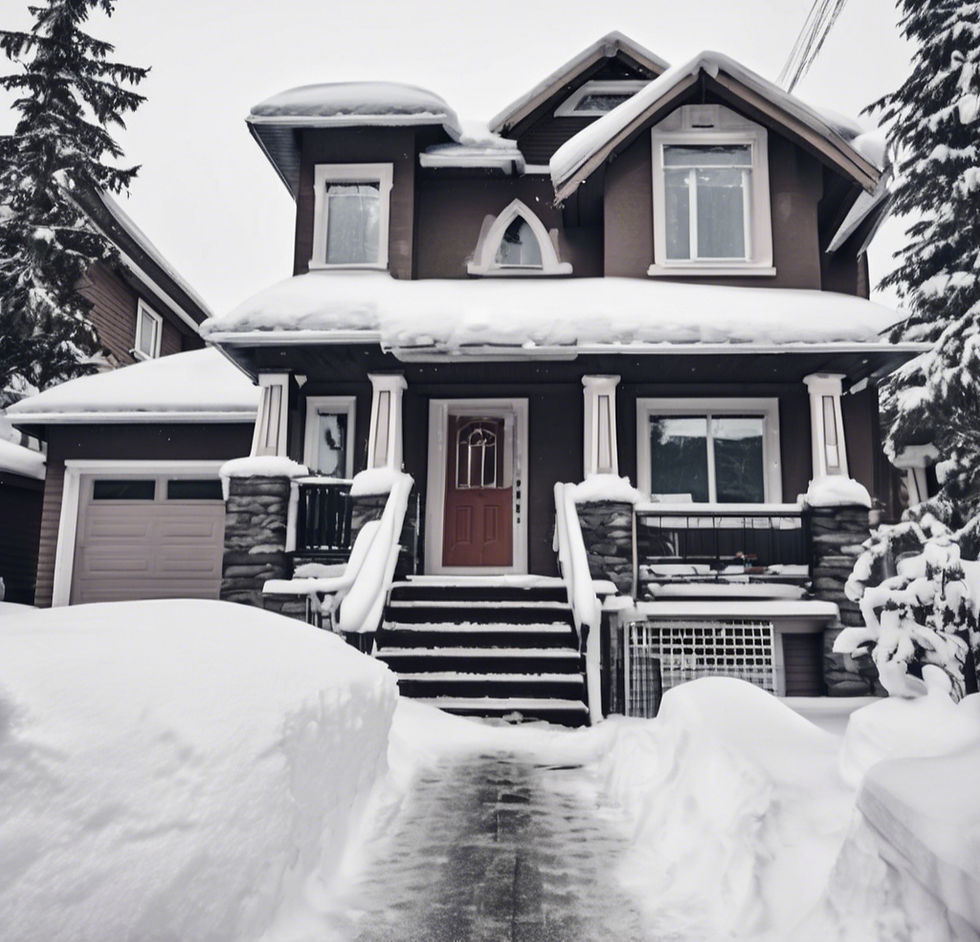
How to Protect Exterior Concrete from Salt Damage
The bad news? Salt damage starts early and moves fast. The good news? It’s preventable—if you take the right steps. Whether you’re building new or trying to protect what you already have, here’s how to keep your concrete from turning into a crumbling mess every spring.
Start with the Right Concrete Mix
It all begins at the pour. If your concrete wasn’t designed for winter, no amount of sealing later will fully make up for it. For exterior slabs in cold climates like northern BC, you need a minimum of 32 MPa compressive strength and, most importantly, air entrainment. Those microscopic air pockets give freezing moisture a place to expand without busting the concrete from the inside out.
If you’re pouring a new driveway, walkway, or patio—make sure your contractor knows this isn’t optional. A weak or improperly batched mix is setting you up for failure before the first frost even hits.
Proper Finishing and Curing
Concrete finishing is an art and a science. Overworked surfaces, troweled too tight, will trap bleed water and lead to surface scaling. On the flip side, under-finishing leaves the surface too porous and prone to soaking up salt water like a sponge.
Once finished, curing is critical. That first week determines how strong and durable the slab will be for years to come. It’s especially important in cold weather—concrete that freezes before it cures is permanently compromised. It’s worth using insulated blankets or temporary heat if conditions demand it.
Seal It—With the Right Product
Unsealed concrete is like a paper towel—it absorbs water, salt, oil, and whatever else lands on it. That’s why a high-quality, penetrating sealer is non-negotiable for long-term durability.
We’re not talking about a glossy, wet-look coating. Those can peel and trap moisture underneath. What you want is a silane or siloxane-based sealer—a breathable product that soaks into the slab and chemically bonds to block out water and chloride ions.
Bonus: Penetrating sealers don’t alter the surface texture, so they won’t make your concrete slippery in wet conditions. That’s a big win in icy regions.
Reapply Every Few Years
No sealer lasts forever. Depending on traffic and exposure, plan to reapply every 2 to 3 years. In high-traffic areas—like driveways or commercial walkways—it may need refreshing sooner. You’ll know it’s time when water stops beading on the surface.
Staying ahead of this maintenance is the cheapest way to avoid major repairs down the road.
Rethink Your Winter De-Icing Strategy
Let’s be real—completely avoiding salt isn’t always practical. But you can minimize the damage:
Shovel promptly to remove snow before it compacts and refreezes.
Use less salt, and don’t pile it up in the same spots.
Switch to sand or eco-friendly de-icers (just check they’re concrete-safe).
Rinse off residue in early spring—don’t let salt soak into the slab all season.
Also, avoid de-icers that contain ammonium nitrate or ammonium sulfate—they’re especially aggressive on concrete and should never be used on slabs, sealed or not.
Use Densifiers and Hardeners on Older Slabs
If your concrete is a few years old and already showing signs of wear, it may benefit from a densifier. These are silicate-based treatments that react with the calcium hydroxide in the concrete to form additional C-S-H (calcium silicate hydrate)—essentially hardening the surface and making it more resistant to water and abrasion.
While densifiers won’t waterproof your concrete like a sealer, they can be a smart secondary layer of defense—especially when paired with a penetrating water repellent.
Long-Term Strategy: Maintenance Over Panic
Most people only call a pro after things have gotten out of hand—when the surface is already scaling, pitting, or cracking. But if you take a proactive approach, that slab can last decades longer than one that’s left untreated.
The best defense is a combination of:
A properly installed, air-entrained slab
Routine cleaning and snow removal
Strategic sealing and reapplication
Smart winter product choices
Even if your concrete has already taken some hits, a proper maintenance and repair plan can stop the damage from spreading—and give you years of extra life before replacement becomes necessary.
What to Do If the Damage Is Already Done
So maybe your concrete didn’t get sealed in time. Maybe salt and freeze-thaw cycles have already taken their toll. You’re staring at crumbling edges, scaling patches, or a driveway that looks like it’s been through battle. Now what?
Let’s talk about realistic options—because while not all damage is reversible, there’s almost always a path forward.
Light to Moderate Surface Damage
If your concrete is mostly intact but showing signs of surface distress—like small chips, light flaking, or minor pitting—you’re likely dealing with early-stage salt damage.
The slab underneath is still structurally sound, which means you’ve got options:
Deep pressure washing to remove contaminants and salt buildup
Grinding or shot grinding (we prefer grinding) to smooth out rough areas
Application of densifiers and penetrating sealers to harden and protect the remaining surface
Optional: decorative coatings or overlays to restore appearance and add slip resistance
This kind of restoration work is cost-effective and can add years of life to your concrete—as long as you catch the problem early and stop the cycle of moisture and salt infiltration.

Moderate to Severe Damage
Once the top layer starts to delaminate or break off in larger chunks, you’re looking at resurfacing. This involves grinding down the damaged layer and installing a new surface coating or microtopping that bonds to the existing slab.
Resurfacing is ideal when:
The damage is widespread but the base slab is still structurally solid
You want to restore both function and curb appeal
Full replacement isn’t in the budget (or isn’t yet necessary)
We typically use polymer-modified concrete products that are flexible, strong, and designed to withstand Northern BC winters. These aren’t box-store patch kits—they’re professional-grade systems installed with surface prep that ensures long-term adhesion.
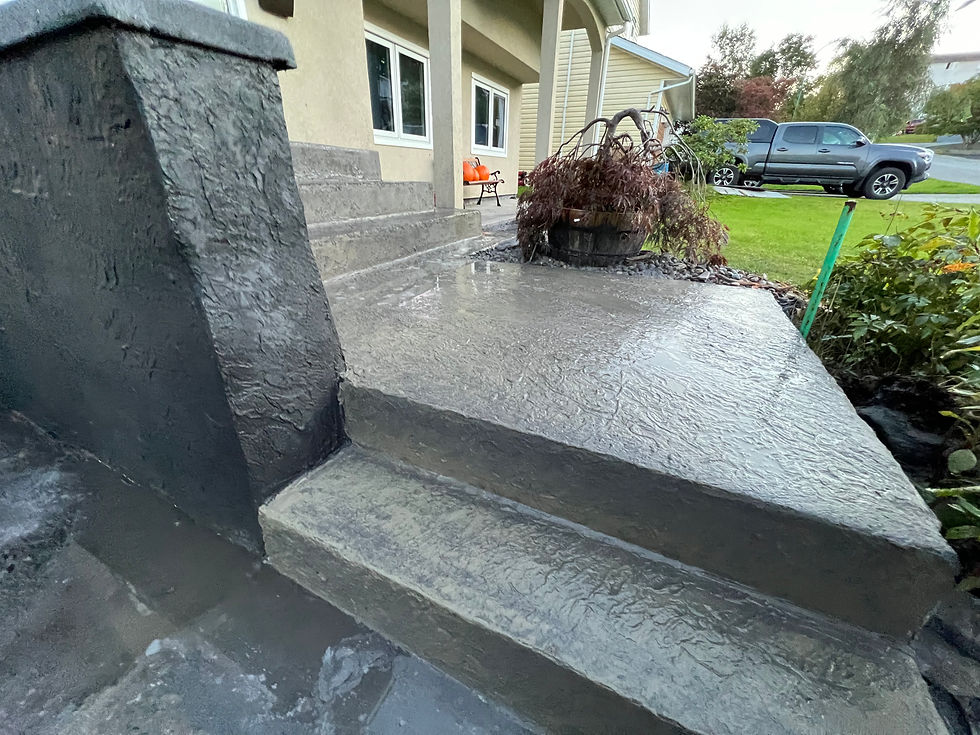
When It’s Time to Replace
Here’s the hard truth: Some concrete just can’t be saved.
If the slab has deep cracks, severe scaling, or widespread structural damage from years of neglect or poor installation, replacement might be your only viable option. In these cases, patching or resurfacing will only offer short-term relief before the deeper issues resurface—often worse than before.
A full tear-out and repour is a bigger investment, but it gives you the chance to do it right: proper mix, air entrainment, reinforced base, curing, sealing, and long-term performance.
Stopgap Measures That Don’t Work
We’ve seen a lot of homeowners try DIY patching compounds from big-box stores. The problem? They rarely hold up through a full freeze-thaw cycle. If the concrete underneath is still soaking up moisture or hasn’t been prepped properly, that patch is going to pop right off—sometimes within weeks.
Likewise, slapping on a surface sealer after major damage won’t reverse the problem. Sealing is a preventative measure, not a cure.
If you're unsure how far gone your concrete is, that’s where a professional inspection makes all the difference. It’s not always about upselling—sometimes it’s just about being honest and giving you real options based on the condition of your slab.
The Executive Surfaces Approach
At Executive Surfaces, we don’t just work with concrete—we work with concrete in northern BC. And that makes all the difference.
The kind of damage we’ve been talking about isn’t theory to us. It’s what we deal with every season. Salt-damaged driveways, flaking steps, patios breaking down before their time—we’ve seen it all, and we know what works in our region’s unforgiving climate.
We take a prevention-first mindset, but we’re also realists. If your concrete is already damaged, we’ll walk you through your options—honestly, without pressure. Sometimes a proper grind and seal is all you need. Other times, a full resurfacing or even replacement is the only long-term fix. We’ll tell you straight and back it up with the work.
Here’s what sets us apart:
We use grinding—and shot blasting—for prep, which gives better adhesion and a cleaner finish.
We only install high-performance resin presealers and resurfacing systems—no corner-cutting, no gimmicks.
We are experienced, and fully insured. We take pride in our work because we live here too.
And most importantly, we don’t treat your project like a job—we treat it like an investment we’re helping protect.
Whether you’re in Terrace, Prince Rupert, or Kitimat, we bring the same level of care to every slab we touch. From new pours to decades-old concrete that’s been through a few too many winters, we’ll help you find the best path forward—and make sure it lasts.
Let’s Get Your Concrete Back on Track
If your concrete is already showing signs of damage—don’t wait for it to get worse. Salt, moisture, and freeze-thaw cycles won’t take the year off. Every season you delay just makes the fix harder and more expensive.
Whether you need a long-lasting sealer, a full resurfacing system, or just some honest advice about what’s possible, Executive Surfaces is here to help.
We’ve worked on concrete all across northern BC—and we know how to protect it from what this climate throws at it. No guesswork. No one-size-fits-all solutions. Just solid work, done right.
Call James at (250) 975-1056 or fill out our contact form to book a site visit. We’ll take a look, answer your questions, and walk you through your best options—without the sales pitch.
Want to stop the damage before next winter? Let’s talk.
Comments